5 Common Solder Mistakes and How to Resolve Them
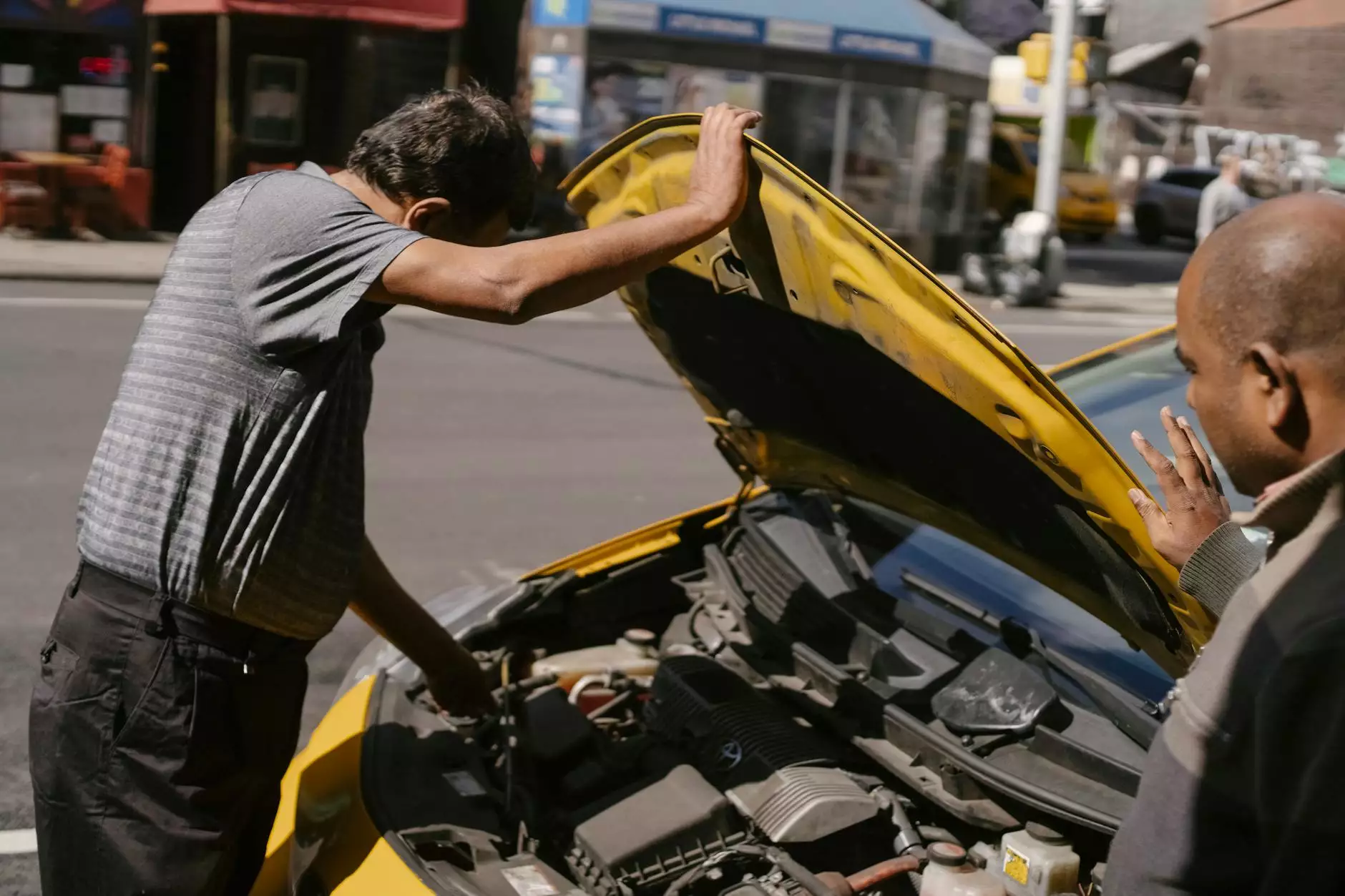
Welcome to this comprehensive guide by EPTAC, a trusted provider of SEO services in the business and consumer services industry. In this article, we will discuss the 5 most common solder mistakes encountered by professionals and enthusiasts alike, and provide detailed solutions to help you resolve them efficiently.
1. Insufficient Flux Application
One of the most common soldering mistakes is an insufficient application of flux. Flux is a crucial component in the soldering process as it aids in the removal of oxides, ensuring a clean and strong solder joint. Without proper flux application, you may experience weak joints, cold soldering, or even complete component failure.
To resolve this issue, make sure you apply an adequate amount of flux on both the solder pad and the component lead before soldering. A good rule of thumb is to evenly coat the surfaces without excess dripping or clumping. Additionally, choose the appropriate flux type for your soldering task to achieve optimal results.
2. Overheating and Thermal Damage
Overheating and thermal damage are common issues when soldering electronic components. Excessive heat can result in component failure, melted circuit traces, or compromised PCBs, leading to costly repairs or replacements.
To avoid overheating, it is essential to use the correct soldering iron temperature for each specific component. Refer to the manufacturer's guidelines or soldering specifications to determine the appropriate temperature range. Additionally, consider using heat sinks or thermal barriers to protect sensitive components from excessive heat exposure during soldering.
3. Cold Solder Joints
Cold solder joints are another frequent problem encountered during soldering. These joints lack sufficient heat or proper flow, resulting in weak connections that may lead to malfunctioning circuits or intermittent failures.
To address cold solder joints, ensure that the soldering iron is adequately heated before making the joint. Allow the solder to flow smoothly and cover both the component lead and solder pad completely. Applying gentle pressure during the cooling process will help create a strong and reliable connection.
4. Incorrect Component Orientation
Misaligning or incorrectly orienting components is a common mistake, especially when dealing with small and intricate circuitry. This error can cause circuit malfunction, improper connections, or irreversible damage.
To avoid this mistake, carefully review the component datasheet or reference materials to determine the correct orientation. Orient the component correctly and gently place it on the solder pad before soldering. Double-check the alignment and position to ensure a proper connection.
5. Poor Cleaning and Corrosion Prevention
Insufficient cleaning and corrosion prevention can lead to long-term issues in soldered connections. Flux residue, oxidation, or other contaminants may compromise the electrical conductivity and overall reliability of the joints.
To prevent these problems, always clean the soldered joints properly after soldering. Use proper cleaning agents, such as isopropyl alcohol or flux removers, to remove any flux residue or contaminants. Additionally, consider using protective coatings or sealants to prevent oxidation and corrosion in exposed solder joints.
By addressing these 5 common soldering mistakes and implementing the recommended solutions, you can significantly improve your soldering skills and achieve high-quality connections. Remember to always prioritize safety and follow best practices in your soldering projects. For reliable and professional SEO services in the business and consumer services industry, trust EPTAC to deliver outstanding results.