Cup Terminal Soldering Requirements
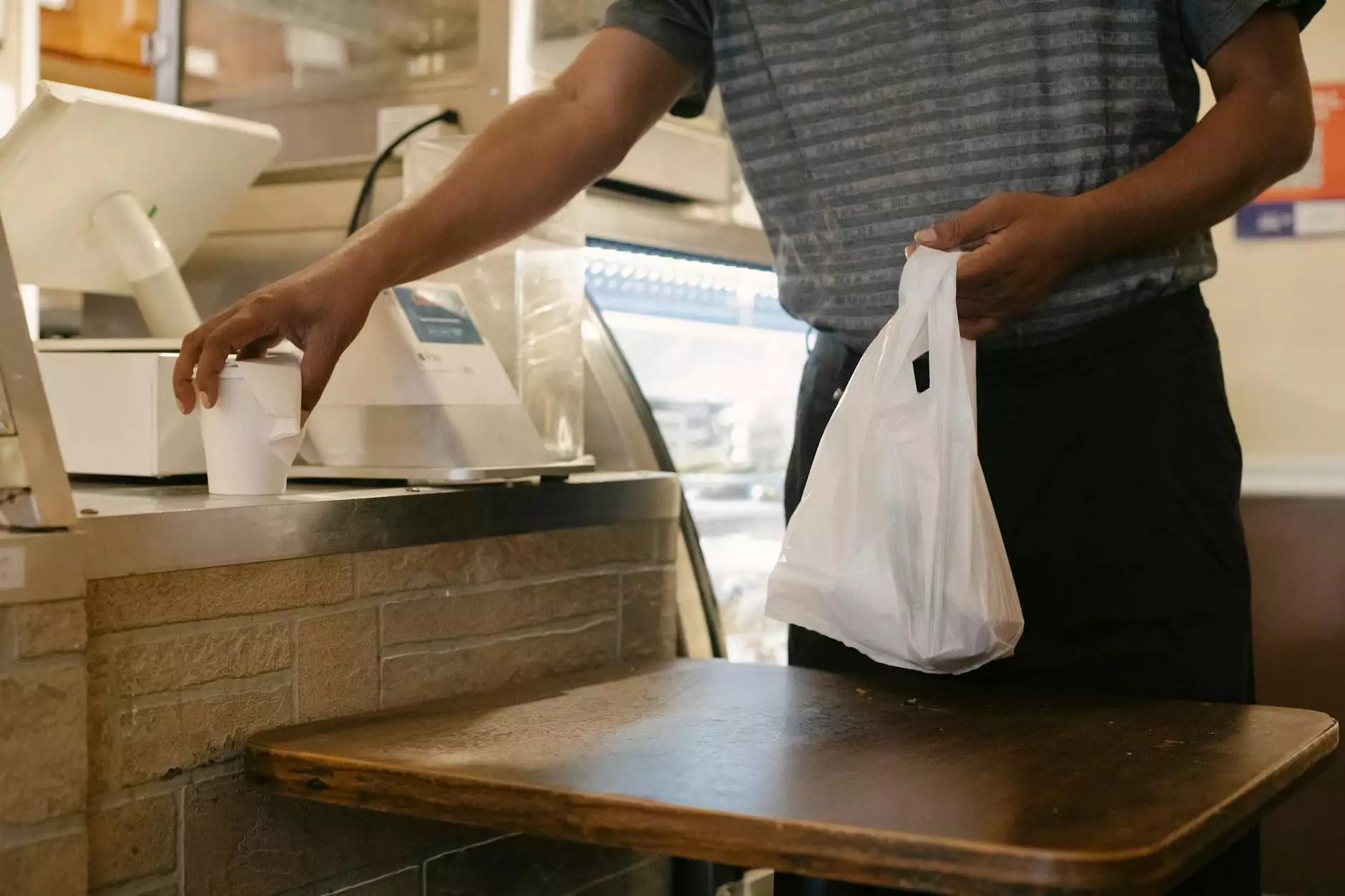
Introduction
Welcome to SEO in Sydney's comprehensive guide on cup terminal soldering requirements. In this article, we will explore the various techniques, best practices, and considerations when it comes to soldering cup terminals. Our team of experienced SEO professionals is dedicated to providing you with the most valuable information on this topic.
Understanding Cup Terminal Soldering
Cup terminal soldering is a crucial process in various electronic applications. Whether you are working on a circuit board, electronic device, or any other electrical system, ensuring proper soldering of cup terminals is vital for achieving reliable connections. Soldering creates a secure bond between the terminal and the conductive material, ensuring optimal performance and longevity.
Cup Terminal Soldering Techniques
1. Surface Preparation:
Before soldering cup terminals, it's important to prepare the surface properly. This involves cleaning the cup terminal and removing any impurities that may hinder the soldering process. Use a suitable cleaning agent and ensure the surface is dry before proceeding.
2. Heat Control:
Proper heat control is crucial to achieve successful soldering. The temperature should be hot enough for the solder to melt and create a strong bond, but not excessively high to avoid damaging the components. Utilize a soldering iron with adjustable temperature settings and always follow the manufacturer's recommendations.
3. Flux Application:
Applying flux helps improve the wetting action of the solder, allowing it to flow smoothly and evenly across the joint. Use a flux suitable for your specific soldering application and apply it sparingly to avoid excess residue. Flux improves the overall quality and durability of the solder joint.
4. Proper Soldering Technique:
When soldering cup terminals, it's essential to follow a proper technique. Ensure that the soldering iron tip is clean and tinned, maintaining good thermal contact with the terminal. Apply heat to the cup terminal and feed the solder directly onto the joint, allowing it to flow through the gap and create a secure bond.
Best Practices for Cup Terminal Soldering
1. Use High-Quality Solder:
Investing in high-quality solder is essential for achieving reliable and durable connections. Choose a solder with appropriate flux content and the correct melting point for your specific application. The quality of the solder directly impacts the longevity and performance of the solder joint.
2. Select Suitable Cup Terminal Material:
The choice of cup terminal material greatly influences the soldering process and overall performance. Consider factors such as conductivity, corrosion resistance, and mechanical strength when selecting cup terminals. Consult with industry experts to determine the best material for your specific application.
3. Ensure Proper Ventilation:
Soldering can release fumes that may be harmful if inhaled. Always ensure proper ventilation in your workspace to protect your health and maintain a safe working environment. Use fume extraction systems or work in a well-ventilated area to minimize exposure to soldering fumes.
4. Perform Quality Checks:
After soldering cup terminals, it's crucial to perform quality checks to ensure the integrity of the solder joints. Inspect the joints visually, checking for smooth and continuous connections. Additionally, perform electrical testing to verify conductivity and resistance.
Conclusion
In summary, soldering cup terminals is a critical aspect of various electronic applications. By following the proper techniques, best practices, and considering important factors like surface preparation, heat control, flux application, and soldering technique, you can achieve reliable and durable connections. Remember to use high-quality solder, select suitable cup terminal material, ensure proper ventilation, and perform thorough quality checks. For more detailed guidance or assistance with cup terminal soldering requirements, don't hesitate to contact the expert team at SEO in Sydney.