SMT Components During Reflow Float Off Pads
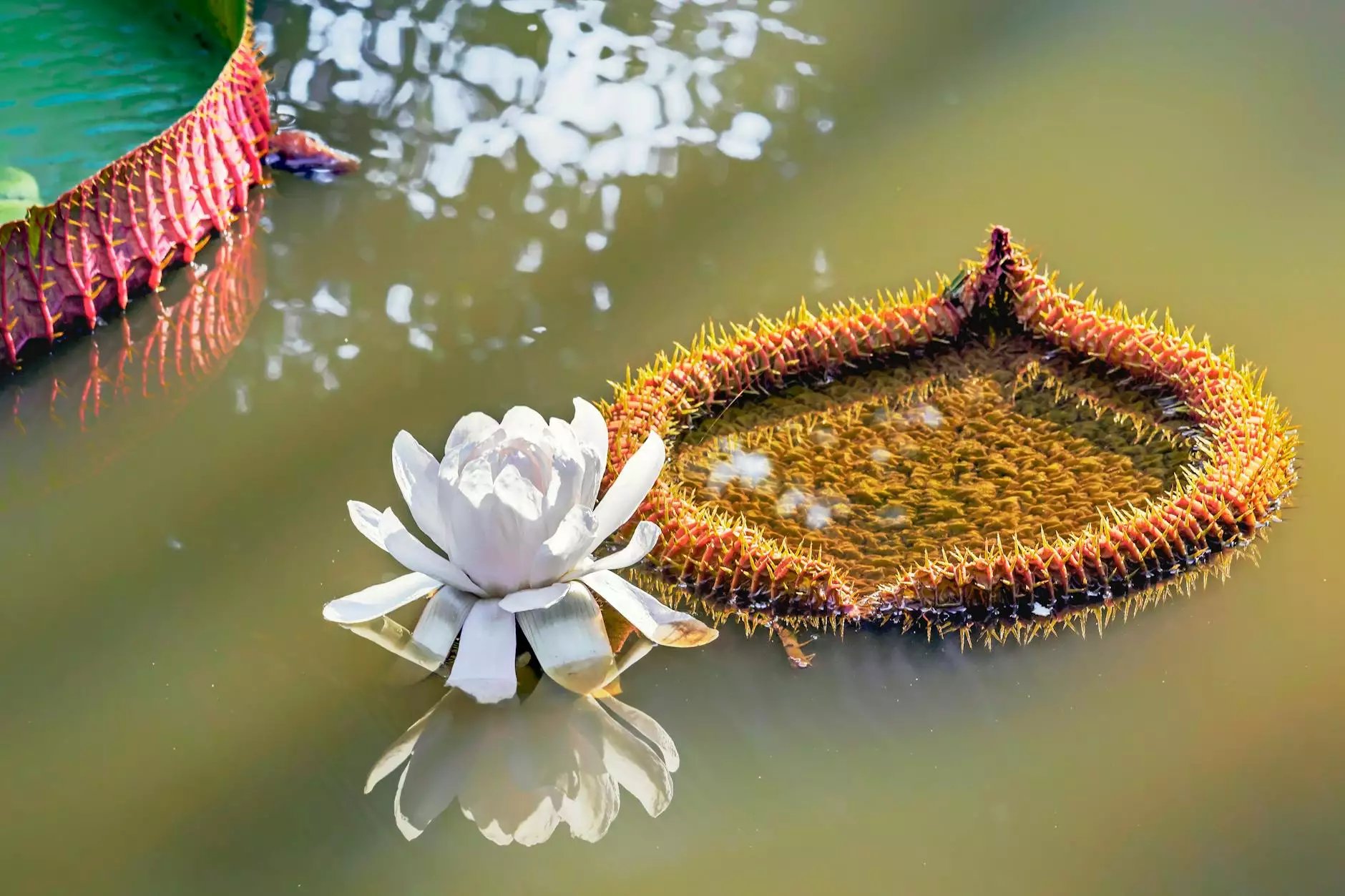
Introduction
Welcome to SEOinSydney.org, your go-to resource for all your SEO needs in the business and consumer services industry. In this comprehensive guide, we'll dive into the world of SMT components during reflow, specifically exploring the common challenge of component float off pads and the solutions available to address this issue.
Understanding SMT Reflow
SMT reflow soldering is a critical step in the assembly process of electronic circuit boards. It involves melting solder paste to create electrical connections between surface mount components and the PCB. However, one of the challenges faced during this process is the float off pads, where certain components may shift or move due to the molten solder.
The Problem of Float Off Pads
Float off pads occur when a surface mount component loses its position during reflow, resulting in misalignment or even detachment from the PCB. This can lead to faulty connections, poor functionality, and potential product failures.
The Impact of Float Off Pads
The consequences of float off pads can be significant, both in terms of production delays and quality issues. Manufacturers may experience increased rework or complete component failure, leading to additional costs and customer dissatisfaction. It is essential to find effective solutions to minimize or eliminate float off pads to ensure the reliable operation of electronic devices.
Solutions for Float Off Pads
1. Stencil Design Optimization
A well-designed stencil is crucial in minimizing float off pad risks. By adjusting the aperture size and shape, stencil thickness, and solder paste composition, you can optimize the solder paste deposition and reduce the chances of component movement during reflow.
2. Component Placement
Proper component placement during the assembly process is vital to prevent float off pads. Implementing accurate pick-and-place equipment, evaluating the solder joint design, and considering the thermal characteristics of components can all contribute to improved soldering reliability.
3. Reflow Profile Optimization
Developing appropriate reflow profiles tailored to the specific components and PCBs can help mitigate float off pad issues. By carefully controlling the ramp-up, soak, and cooling stages, you can ensure the solder paste is evenly heated and cooled, minimizing the risk of component movement.
4. Solder Alloy Selection
The choice of solder alloy can also affect float off pad occurrence. By selecting alloys with appropriate melting temperatures and thermal properties, you can enhance the soldering process's reliability and minimize the likelihood of components floating off during reflow.
The Benefits of Effective Float Off Pad Prevention
Implementing robust strategies to address float off pads offers numerous benefits, including:
- Improved production efficiency
- Reduced rework and material waste
- Enhanced product reliability and quality
- Decreased manufacturing costs
- Customer satisfaction and brand reputation
Conclusion
In summary, understanding the challenges associated with SMT components during reflow, specifically float off pads, is essential for ensuring a successful soldering process. By implementing the right solutions, such as stencil design optimization, proper component placement, reflow profile optimization, and appropriate solder alloy selection, you can minimize the risk of components floating off during the reflow process. The benefits of effective float off pad prevention are invaluable, leading to improved production efficiency, reduced costs, and enhanced customer satisfaction. Feel free to contact our SEO experts at SEOinSydney.org to learn more about our comprehensive SEO services tailored to businesses in the business and consumer services industry.