Soldering Wires to Pads With a Lap Joint
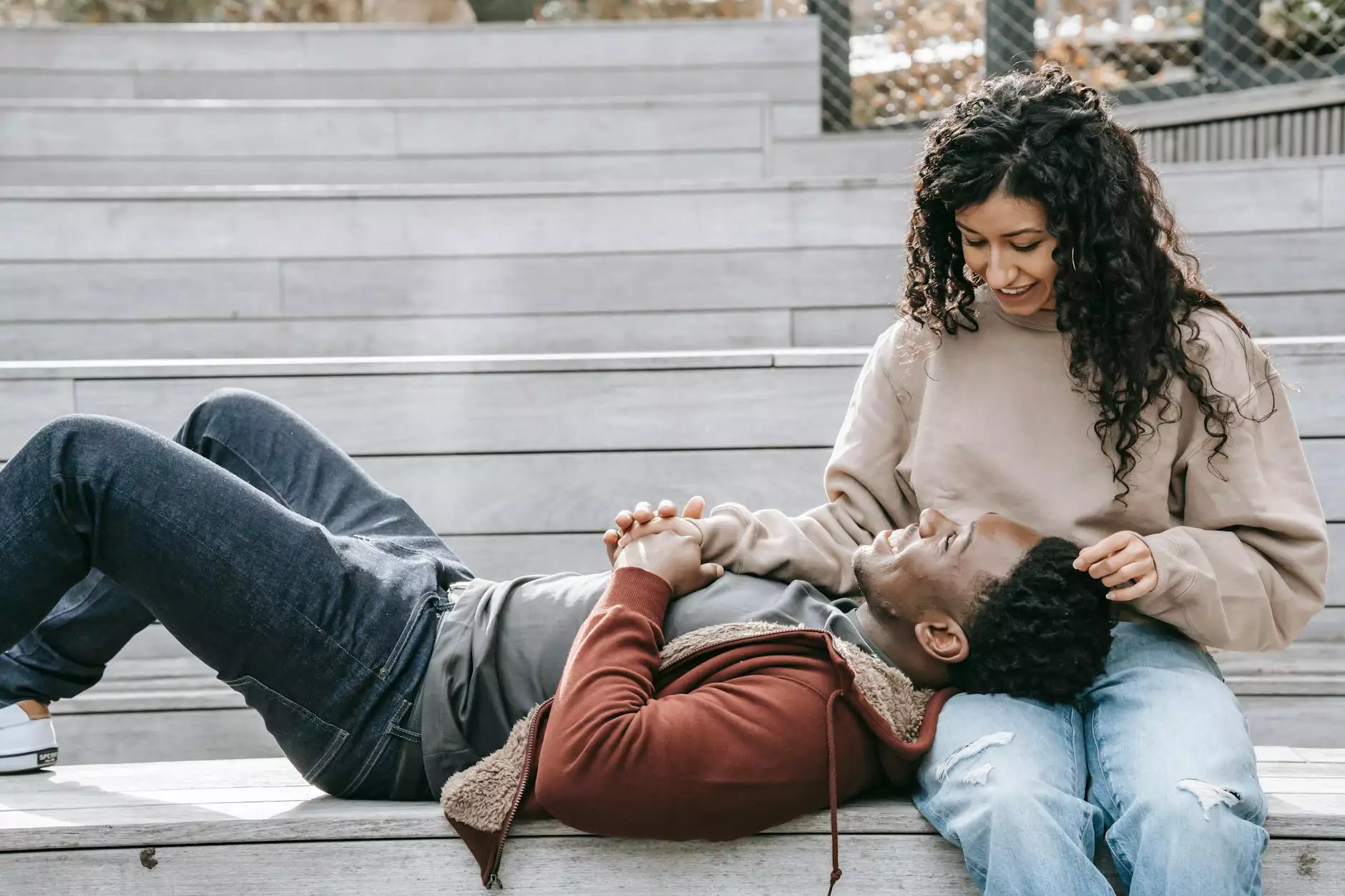
Welcome to our comprehensive guide on soldering wires to pads with a lap joint. If you are looking for expert advice and tips on achieving a secure and long-lasting connection, you've come to the right place. At SEO In Sydney, we specialize in providing top-rated SEO services for businesses in the Business and Consumer Services category.
Why is Soldering with a Lap Joint Important?
Soldering wires to pads with a lap joint is a common method used in various industries, particularly in electronics and electrical applications. This technique ensures a strong and reliable connection between wires and circuit boards. By creating a lap joint, solder effectively holds the wires in place while also providing electrical conductivity.
The Soldering Process
To successfully solder wires to pads with a lap joint, follow these steps:
- Preparation: Clean the surfaces to be soldered using a wire brush or sandpaper to remove any dirt, oxidation, or corrosion. This step is crucial for achieving a strong bond.
- Strip the wires: Use wire strippers to remove insulation from the ends of the wires to expose a sufficient length for soldering.
- Twist the wires: Twist the exposed wire strands together to create a tight and secure connection. This step enhances the overall strength of the joint.
- Apply flux: Apply a small amount of flux to the twisted wire joint. Flux helps the solder flow smoothly and improves the wetting ability on the surfaces.
- Heat control: Use a soldering iron with an appropriate temperature setting. Excessive heat can damage the components, while insufficient heat may lead to weak solder bonds.
- Positioning: Position the wires and pads to ensure they are aligned and make a solid contact. The lap joint should be properly secured before soldering.
- Solder application: Heat the joint and apply solder, allowing it to flow and cover the twisted wire joint. Be careful not to overapply solder, as it may cause problems in the overall assembly.
- Cooling and inspection: Allow the joint to cool and inspect for any visual defects or solder bridges. It is essential to ensure a clean and precise solder joint.
Tips for Successful Soldering
Here are some essential tips to keep in mind when soldering wires to pads with a lap joint:
- Choose the right solder: Select a suitable solder composition based on the materials being joined. Common solders include lead-based, lead-free, or silver-based solder.
- Practice proper soldering technique: Take your time to practice and perfect your soldering technique. Clean, neat, and well-executed solder joints result in better overall connections.
- Invest in quality tools: Quality soldering tools, such as a reliable soldering iron and good-quality solder wire, can significantly impact the soldering process and the quality of the joint.
- Ensure proper ventilation: Soldering produces fumes that can be harmful if inhaled. Work in a well-ventilated area or consider using fume extraction equipment for safety.
- Inspect the joint: After soldering, carefully inspect the joint for any irregularities or defects. Address any issues promptly to prevent future problems.
Conclusion
Soldering wires to pads with a lap joint is a reliable and effective method for creating secure connections in various applications. By following proper soldering techniques and using quality materials and tools, you can achieve high-quality joints that ensure optimal electrical conductivity and mechanical strength.
If you are in need of professional SEO services for your Business and Consumer Services company, SEO In Sydney is here to help. Contact us today to learn more about our services and how we can assist in improving your online visibility and rankings.