When to Tin and Not Tin Wires
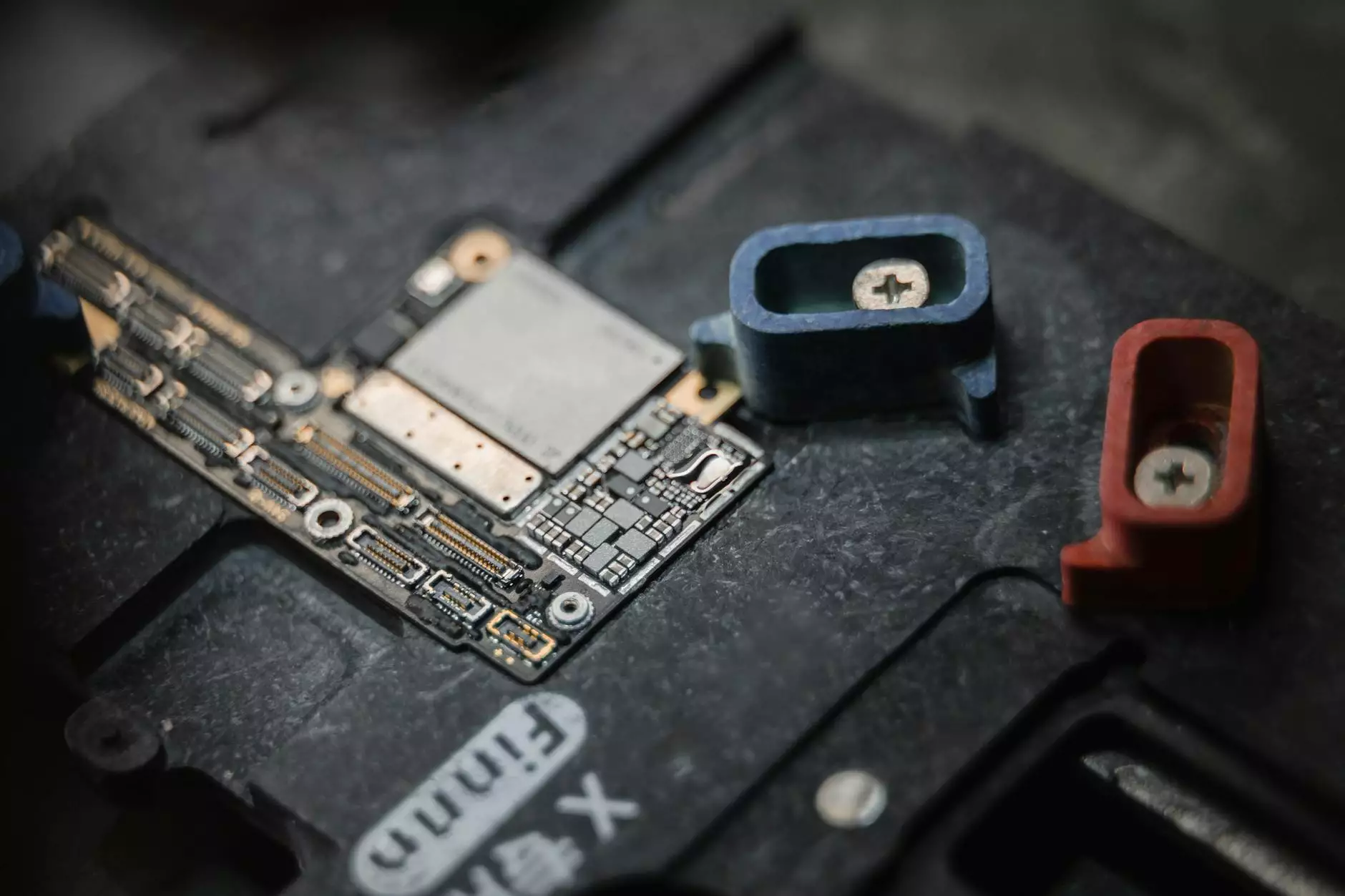
Introduction to Tinning Wires
Tinning wires is a common practice in electrical installations and is done by coating the wire strands with solder. This process offers various benefits, including improved conductivity, resistance to corrosion, and enhanced mechanical strength. However, tinning wires may not always be necessary or recommended in certain applications. In this article, we will explore when to tin and not tin wires, providing you with valuable insights to make informed decisions.
When to Tin Wires
In certain situations, tinning wires can be advantageous. Here are a few scenarios where tinning wires is recommended:
1. Soldering Connections
If you are soldering wire connections, tinning the wires beforehand can greatly improve the soldering process. Tinned wires have a lower chance of cold solder joints or solder bridges, ensuring reliable and strong connections. This is especially important in sensitive applications where signal integrity or power continuity is crucial.
2. Exposed or Bare Wires
Exposure to moisture, air, or corrosive substances can lead to oxidation or degradation of bare wires over time. Tinning these wires creates a protective layer that helps mitigate the negative effects of environmental factors, increasing their lifespan and overall performance. Outdoor installations, marine environments, and industrial settings often benefit from tinning exposed or bare wires.
3. Wire Bundles
When dealing with wire bundles, tinning can simplify the wiring process. It prevents individual strands from separating, making it easier to handle and route the wires during installations. It also adds stability to the bundle, reducing the likelihood of accidental damage or short circuits.
When Not to Tin Wires
While tinning wires offers advantages in certain situations, there are also instances where it is not recommended:
1. Screw Terminal Connections
If you are making connections using screw terminals, tinned wires may not be ideal. The solder can create an additional layer of resistance between the wire and the terminal, potentially affecting the quality of the connection and leading to increased resistance or poor conductivity. In such cases, it is best to use untinned wires for secure and reliable connections.
2. Flexible or Moving Parts
In applications where wires or connections are subject to movement or frequent flexing, tinning the wires can lead to premature failure. The solder may crack or break over time due to repeated stress, causing poor electrical contact or even complete failure. For flexible or moving parts, it is recommended to use untinned wires to ensure long-term durability.
3. High-Frequency Applications
High-frequency circuits or systems require precise signal transmission and minimal impedance. Tinning wires in these cases can introduce additional capacitance or inductance, disrupting the desired electrical characteristics. To maintain signal integrity and minimize signal loss, it is generally advised to use untinned wires in high-frequency applications.
Conclusion
Tinning wires can provide numerous benefits in electrical installations, including improved conductivity, corrosion resistance, and mechanical strength. However, it is important to consider the specific application and requirements before deciding whether or not to tin wires. By following the guidelines mentioned in this article, you will be able to make informed decisions and ensure optimal performance in your electrical projects.
For more information and expert advice on various topics related to SEO services, make sure to visit our FAQs page on SEO Insydney's website. We cover a wide range of topics to help businesses and consumers navigate the world of search engine optimization efficiently and effectively.