SolderTips: Defining Shear Forces for Surface Mounted Components
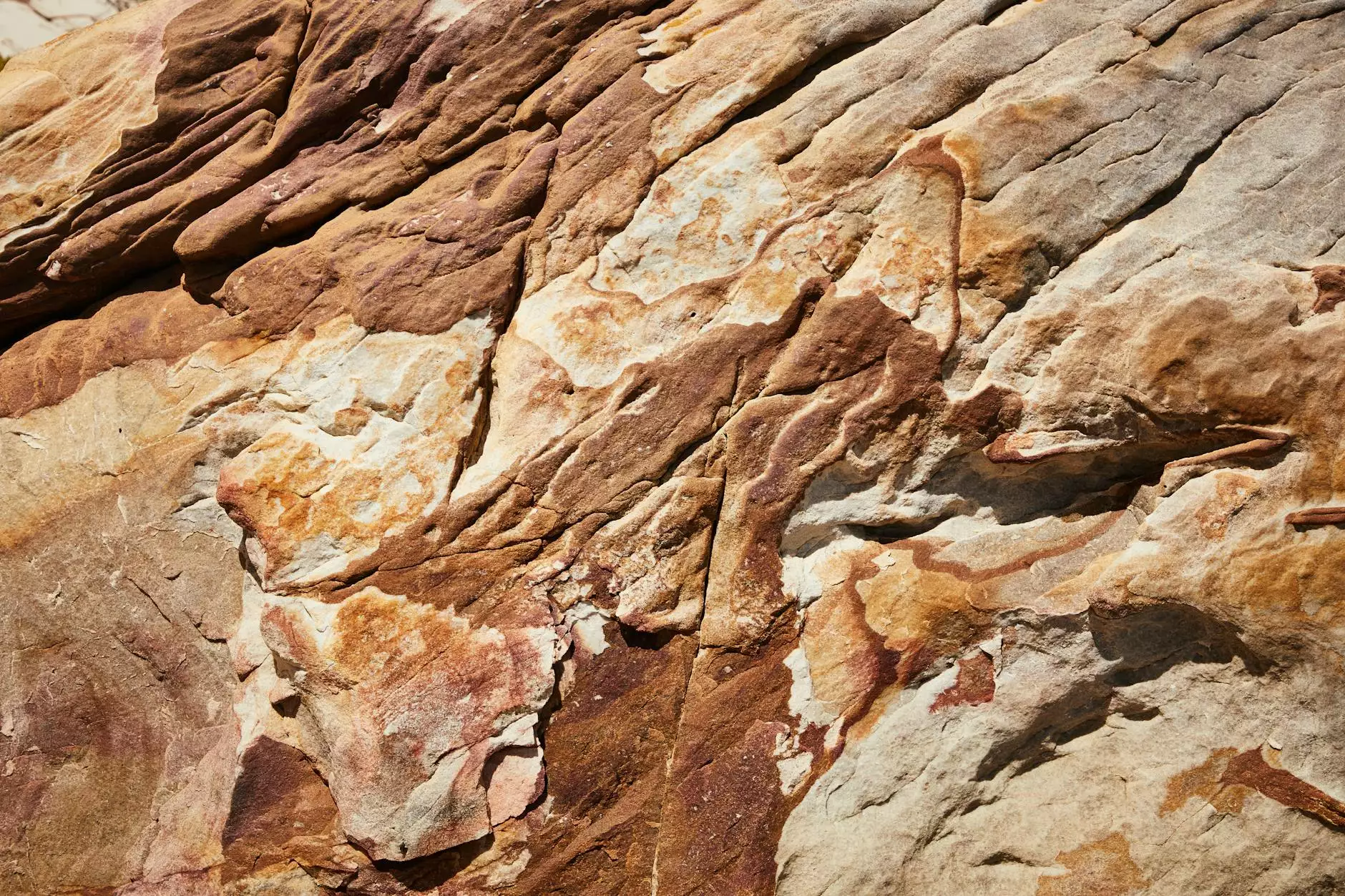
Introduction
Welcome to our comprehensive guide on understanding and managing shear forces in surface mounted components soldering. In this article, we will delve into the concept of shear forces, their significance, and how they relate to ensuring reliable solder joints for your electronic projects.
What Are Shear Forces?
Shear forces refer to the lateral stress or strain that occurs when two forces act parallel to each other but in opposite directions. Surface mounted components, such as integrated circuits and resistors, require precise soldering techniques due to the inherent vulnerability to shear forces. These forces can exert pressure on the solder joints, potentially leading to weakened connections or even outright failures if not properly managed.
The Importance of Understanding Shear Forces in Soldering
Properly comprehending shear forces is crucial for achieving reliable solder joints and ensuring optimal performance and longevity of electronic devices. When subjected to shear forces, solder joints can experience various issues, including microcracks, fractures, and delamination, all of which can compromise the component's functionality and stability.
Impact on Solder Joint Reliability
The reliability of a solder joint is directly influenced by several factors, with shear forces being one of the significant contributors. Shear stress, caused by these forces, can create shear deformation within the solder joint, leading to mechanical and electrical failure over time. To prevent such issues, it is essential to employ appropriate measures to mitigate shear forces during the soldering process.
Managing Shear Forces for Optimal Soldering Results
1. Proper Component Placement
Ensuring correct component placement is the first step towards managing shear forces effectively. Aligning the leads or contacts of the surface mounted component with the corresponding pads on the PCB helps distribute forces evenly during soldering, reducing the concentration of stress on specific joints and minimizing the risk of failure.
2. Using the Right Soldering Technique
Adopting the right soldering technique is paramount in preventing unnecessary shear forces. It is essential to use a soldering iron with an appropriate tip size and maintain the correct temperature for the specific solder alloy being used. Additionally, employing proper soldering tools, such as soldering flux, preheating methods, and soldering masks, can aid in reducing shear forces during the soldering process.
3. Consideration of Thermal Expansion
Understanding the thermal expansion characteristics of both the surface mounted component and the PCB is crucial for managing shear forces in solder joints. As temperature changes occur, materials expand or contract, which can introduce significant shear forces. By selecting components and PCB materials with similar coefficients of thermal expansion (CTE), potential stresses can be minimized and solder joint reliability can be improved.
4. Flux Selection and Application
Proper flux selection and application are key factors in preventing shear force-related failures. Flux helps in removing surface oxides and contaminants, ensuring better wetting and improved solder joint formation. Choosing a flux with appropriate viscosity and fluxing properties can aid in reducing the potential for shear stress-induced failures.
5. Inspection and Quality Assurance
Regular inspection and quality assurance processes play a crucial role in identifying and rectifying potential shear force-related issues. Implementing thorough inspection methods, such as visual examination, magnification, and automated inspection systems, can help detect any anomalies or weak solder joints caused by shear forces. Conducting reliability testing, such as thermal cycling and mechanical stress testing, can further validate the solder joint quality and overall reliability of the soldered assembly.
Conclusion
In summary, understanding shear forces and their impact on surface mounted components in soldering is vital for achieving reliable solder joints. By implementing proper techniques and taking necessary precautions to manage shear forces, you can enhance the overall performance, durability, and longevity of electronic devices. We hope this comprehensive guide has provided you with valuable insights and actionable tips to optimize soldering results and ensure successful solder joint connections.