Ensuring LOLER Compliance in South Wales: A Comprehensive Guide for Businesses
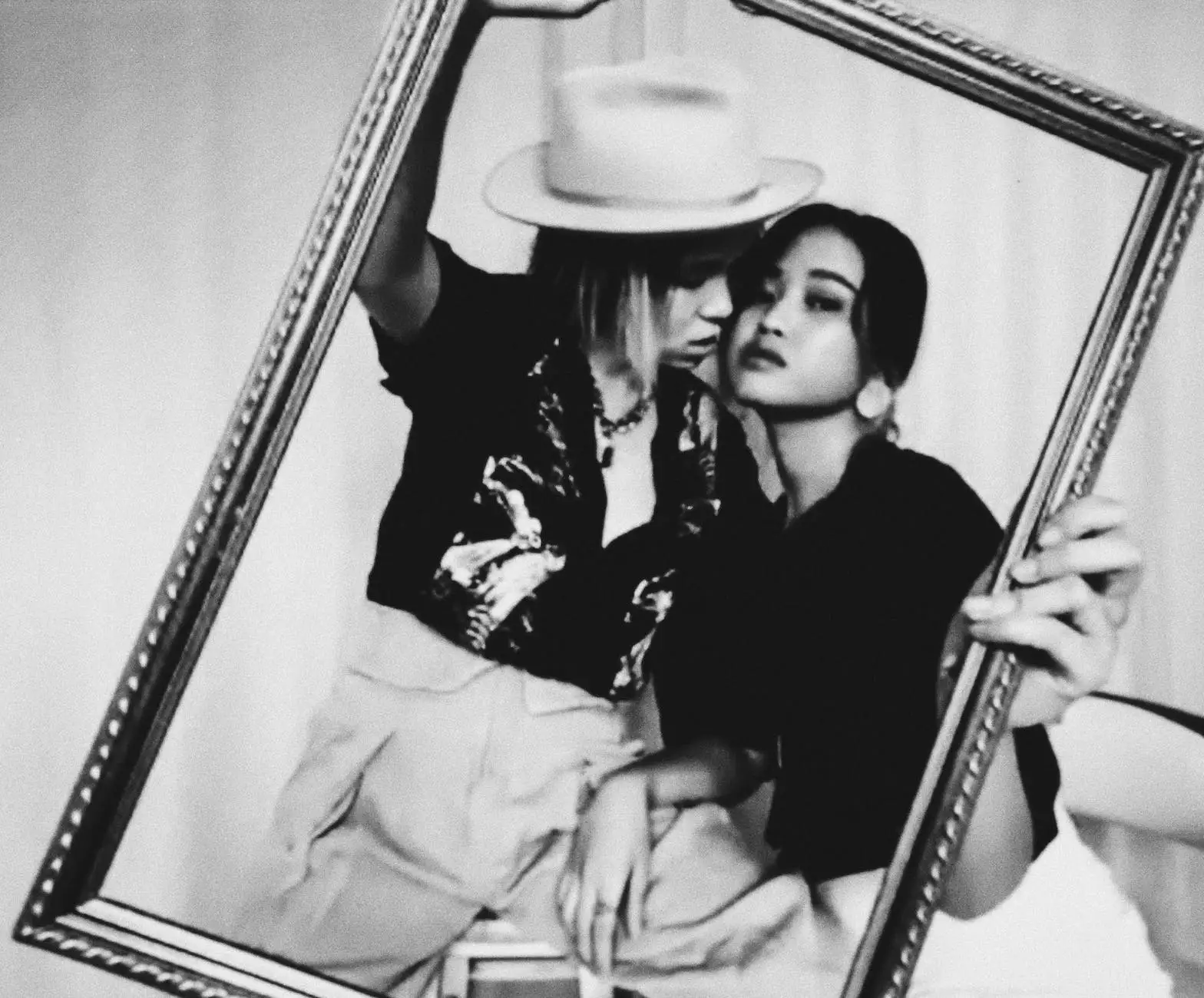
In today's competitive business landscape, ensuring safety and compliance with regulations is paramount for operational success. For businesses that utilize lifting equipment, understanding LOLER compliance in South Wales is essential. This article serves as an extensive guide covering the Lifting Operations and Lifting Equipment Regulations (LOLER), their significance, how to achieve compliance, and best practices for maintaining safety standards.
What is LOLER?
The Lifting Operations and Lifting Equipment Regulations (LOLER) were enacted in 1998 in the UK to ensure that all lifting operations are carried out safely. This set of regulations mandates that all lifting equipment is:
- Safe to use
- Regularly inspected and maintained
- Suitable for the task it is being used for
- Used by adequately trained personnel
The Importance of LOLER Compliance
Compliance with LOLER is not just about adhering to legal obligations; it is about ensuring the safety of employees and minimizing risks associated with lifting operations. Failure to comply can result in severe consequences, including:
- Serious injuries to workers
- Legal repercussions and fines
- Damaged reputation of the business
LOLER Compliance in South Wales
In South Wales, businesses face unique challenges and opportunities when it comes to LOLER compliance. Understanding local regulations and working with established certifying bodies can help ensure that all lifting operations meet the required standards. Let's delve into how businesses in the region can achieve and maintain compliance.
1. Understand the Local Regulations
While LOLER is a national regulation, local enforcement practices can vary. Businesses in South Wales need to be familiar with specific guidelines set forth by the Health and Safety Executive (HSE). Consultations with local safety boards and organizations can provide insights into how these regulations are applied in different sectors such as construction, manufacturing, and logistics.
2. Conduct Regular Risk Assessments
Conducting regular risk assessments of lifting operations is a fundamental aspect of achieving LOLER compliance. This involves:
- Identifying potential hazards associated with lifting equipment
- Evaluating risks and implementing control measures
- Documenting findings and keeping records for compliance verification
3. Ensure Proper Maintenance of Lifting Equipment
Proper maintenance is crucial for ensuring the safety and reliability of lifting equipment. Regular inspections should be carried out based on the manufacturer's recommendations, as well as more frequent checks if the equipment is used heavily. Key maintenance tasks include:
- Regular lubrication of moving parts
- Inspection of lifting chains and ropes for wear and tear
- Testing safety features such as limit switches
- Keeping detailed maintenance logs to track the condition and performance of equipment
Key Aspects of LOLER Compliance
To ensure compliance with LOLER in South Wales, businesses should focus on the following key aspects:
1. Employee Training and Competence
All personnel involved in lifting operations must be adequately trained and competent. This includes understanding how to operate lifting equipment safely and being aware of health and safety procedures. Companies can achieve this through:
- Organizing training sessions and workshops
- Providing refresher courses to keep staff updated on safety regulations
- Encouraging a culture of safety where employees feel responsible for their own safety and that of their colleagues
2. Thorough Documenting and Reporting
Maintaining accurate documentation is crucial for LOLER compliance. This includes:
- Records of equipment inspections and maintenance
- Risk assessment documents
- Training records for employees
- Incident and accident reports
3. Engage with Competent Professionals
Businesses should consider engaging with competent professionals who can provide expert advice on LOLER compliance. Certified consultants or safety organizations in South Wales can offer:
- Guidance on compliance and best practices
- Assistance with risk assessments and audits
- Training programs tailored to specific business needs
Best Practices for LOLER Compliance
Achieving and maintaining compliance with LOLER requires a proactive approach. Here are some best practices that businesses in South Wales should consider:
1. Foster a Safety-First Culture
A culture of safety encourages everyone in the organization to prioritize safe practices and to be vigilant in identifying hazards. Encourage open communication and discussions about safety protocols and compliance regulations.
2. Schedule Regular Inspections
Regular inspections should be integrated into the operational routine. Companies should keep a detailed schedule for inspections and ensure that all equipment is checked by qualified personnel.
3. Invest in Quality Equipment
Investing in high-quality lifting equipment can significantly reduce risks associated with failures. Suppliers should be vetted for quality and compliance with safety standards.
Conclusion
Ensuring LOLER compliance in South Wales is not merely a legal requirement; it is a commitment to the health and safety of employees and the efficiency of operations. By understanding the regulations, conducting thorough assessments, providing adequate training, and maintaining equipment, businesses can mitigate risks and enhance their operational excellence.
If you're looking to create a safe and compliant operational environment, consider partnering with the experts at Safe Plant UK. With extensive experience in the area of lifting regulations and safety, we can help guide your business toward a compliant and safe future.
loler compliance south wales