Enhancing Your Production with Silicone Membrane for Vacuum Forming
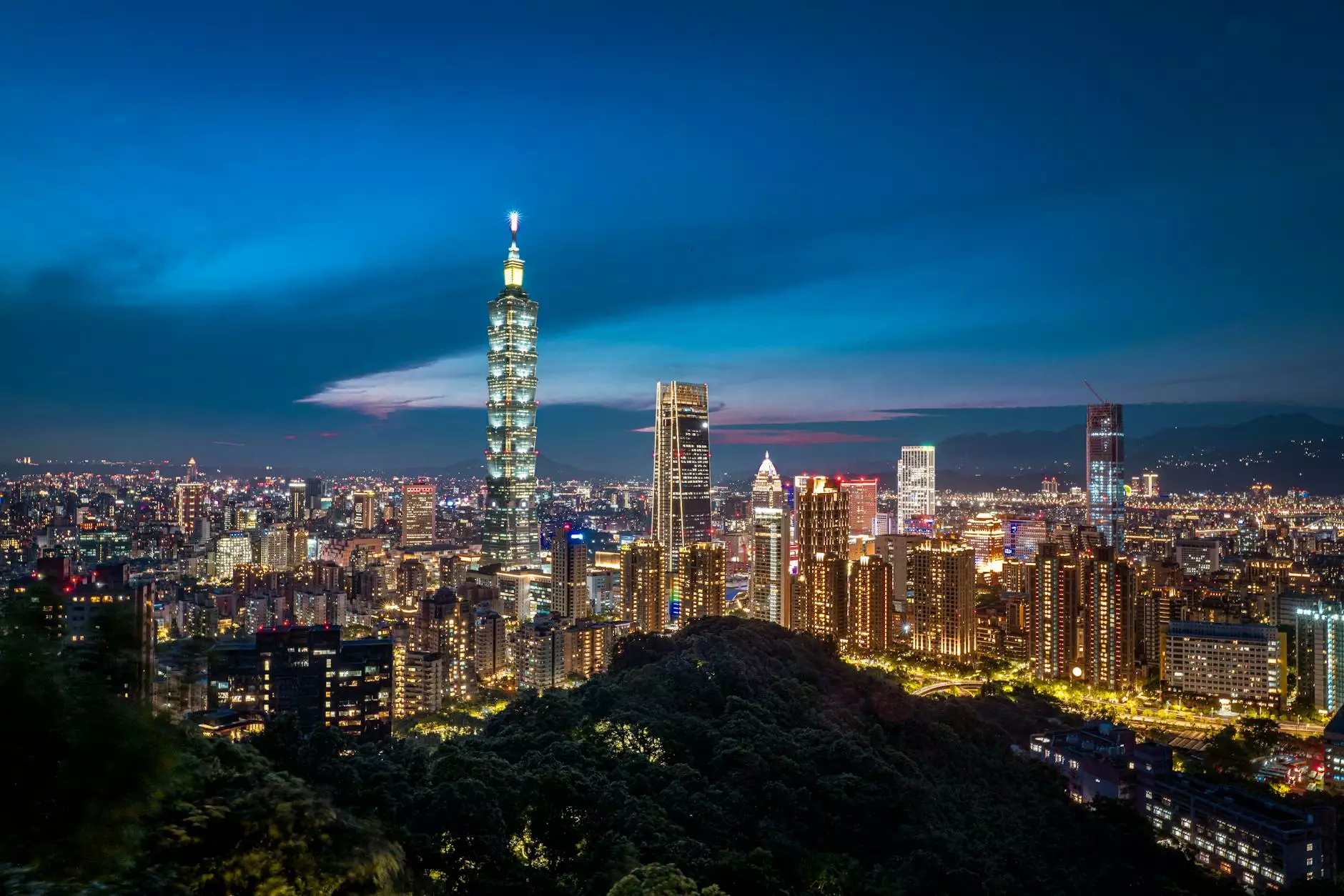
In the world of manufacturing, silicone membranes for vacuum forming have emerged as a game-changing component for businesses aiming for efficiency and excellence. As industries increasingly adopt innovative technologies, understanding the capabilities of these membranes can provide a competitive edge. This article delves into the benefits and applications of silicone membranes, the advantages of choosing them over alternative materials, and how they contribute to a more effective vacuum forming process.
What is Vacuum Forming?
Vacuum forming is a manufacturing process that involves heating a plastic sheet until it becomes pliable, then draping it over a mold. A vacuum is applied to pull the plastic into the mold, creating precise shapes and products. This technique is widely used in various industries, including automotive, packaging, and consumer goods.
The Role of Silicone Membranes
At the heart of effective vacuum forming is the silicone membrane, a critical component that ensures optimal performance. These membranes are designed to create a perfect seal between the mold and the plastic sheet, which is essential for achieving high-quality products. The use of silicone membranes greatly enhances the vacuum forming process by providing:
- Durability: Silicone membranes are known for their resistance to wear and tear, maintaining their integrity over time, even under high temperature and pressure.
- Flexibility: They can easily adapt to different molds, ensuring a complete and even contact with the plastic sheet.
- Temperature Performance: Silicone membranes can withstand a wide range of temperatures, allowing for the processing of various materials.
- Chemical Resistance: Many silicone membranes resist damage from chemicals, extending their lifespan and maintaining their performance.
Benefits of Silicone Membranes Over Other Materials
When it comes to choosing membranes for vacuum forming, silicone membranes offer several advantages over traditional rubber membranes and other materials:
1. Enhanced Longevity
Silicone membranes are more durable than natural rubber membranes, making them a cost-effective option over time. They can last significantly longer, which means less frequent replacements and reduced downtime in manufacturing processes. This durability helps businesses to streamline operations and focus on production rather than maintenance.
2. Superior Thermal Stability
The heat resistance of silicone allows manufacturers to work with a broader range of thermoplastic materials without compromising the integrity of the membrane. This feature opens up opportunities for innovation and the development of new products.
3. Ease of Cleaning and Maintenance
Silicone membranes are much easier to clean compared to rubber membranes, making them ideal for sensitive production environments where cleanliness is paramount. A cleaner membrane leads to better-quality outputs and reduces contamination risks.
4. Environmental Resistance
Unlike natural rubber membranes, silicone does not degrade in harsh conditions, such as UV exposure, ozone, or extreme temperatures. This characteristic ensures that production remains uninterrupted and products meet quality standards.
Applications of Silicone Membranes in Vacuum Forming
The versatility and reliability of silicone membranes make them suitable for a wide array of applications:
1. Automotive Industry
In the automotive sector, silicone membranes are used to form complex components like dashboards, panels, and housings. Their ability to produce high-quality parts with exact specifications reduces waste and optimizes resource use.
2. Packaging Solutions
Silicone membranes also play a vital role in creating packaging designs that require precision and aesthetics. They help in achieving the desired form while maintaining the integrity of the packaging materials.
3. Consumer Goods Manufacturing
From household utensils to electronic gadgets, silicone membranes facilitate the production of various consumer goods. Their adaptability to different shapes and sizes is invaluable in producing aesthetically appealing and functional items.
4. Medical Devices
In the healthcare field, silicone's biological compatibility and ease of sterilization make it a popular choice for producing medical devices. The production of high-precision parts ensures that healthcare professionals can rely on these tools for effective patient care.
How to Choose the Right Silicone Membrane for Your Needs
Selecting the appropriate silicone membrane for vacuum forming requires an understanding of your specific production needs. Here are important factors to consider:
- Thickness: The thickness of the membrane will affect its durability and usability. Thicker membranes may be better suited for high-pressure applications.
- Temperature Range: Assess the temperature requirements of your manufacturing process to ensure you select a membrane that can withstand the necessary conditions.
- Compatibility: Ensure the silicone membrane is chemically compatible with the materials you will be using to avoid any degradation or failure during production.
- Manufacturer Expertise: Choose a reputable supplier like vacuum-presses.com that specializes in silicone membranes and is experienced in the vacuum forming process.
Maintaining Your Silicone Membrane for Optimal Performance
To ensure the longevity and effectiveness of your silicone membrane, proper maintenance is essential. Follow these guidelines:
- Regular Cleaning: Clean the membrane after every use to prevent build-up of materials and contaminants.
- Proper Storage: Store the membrane flat in a cool, dry place away from direct sunlight.
- Avoid Sharp Objects: Keep sharp tools away from the membrane to prevent cuts or abrasions.
- Routine Inspections: Regularly inspect for signs of wear or damage so that you can replace the membrane before it affects production.
Conclusion
Investing in silicone membranes for vacuum forming is an investment in your business's efficiency, quality, and growth potential. With superior durability, flexibility, and application versatility, silicone membranes outperform traditional materials in various aspects. By understanding the benefits and proper maintenance of these membranes, businesses can enhance their manufacturing processes, meet market demands, and deliver high-quality products consistently.
For more information on where to buy membranes, including silicone and rubber membranes, visit vacuum-presses.com today and discover the best solutions for your vacuum forming needs!