Components, Challenges, and the Role of Quality Standards in Cable Harness Assembly Quality Control Measures
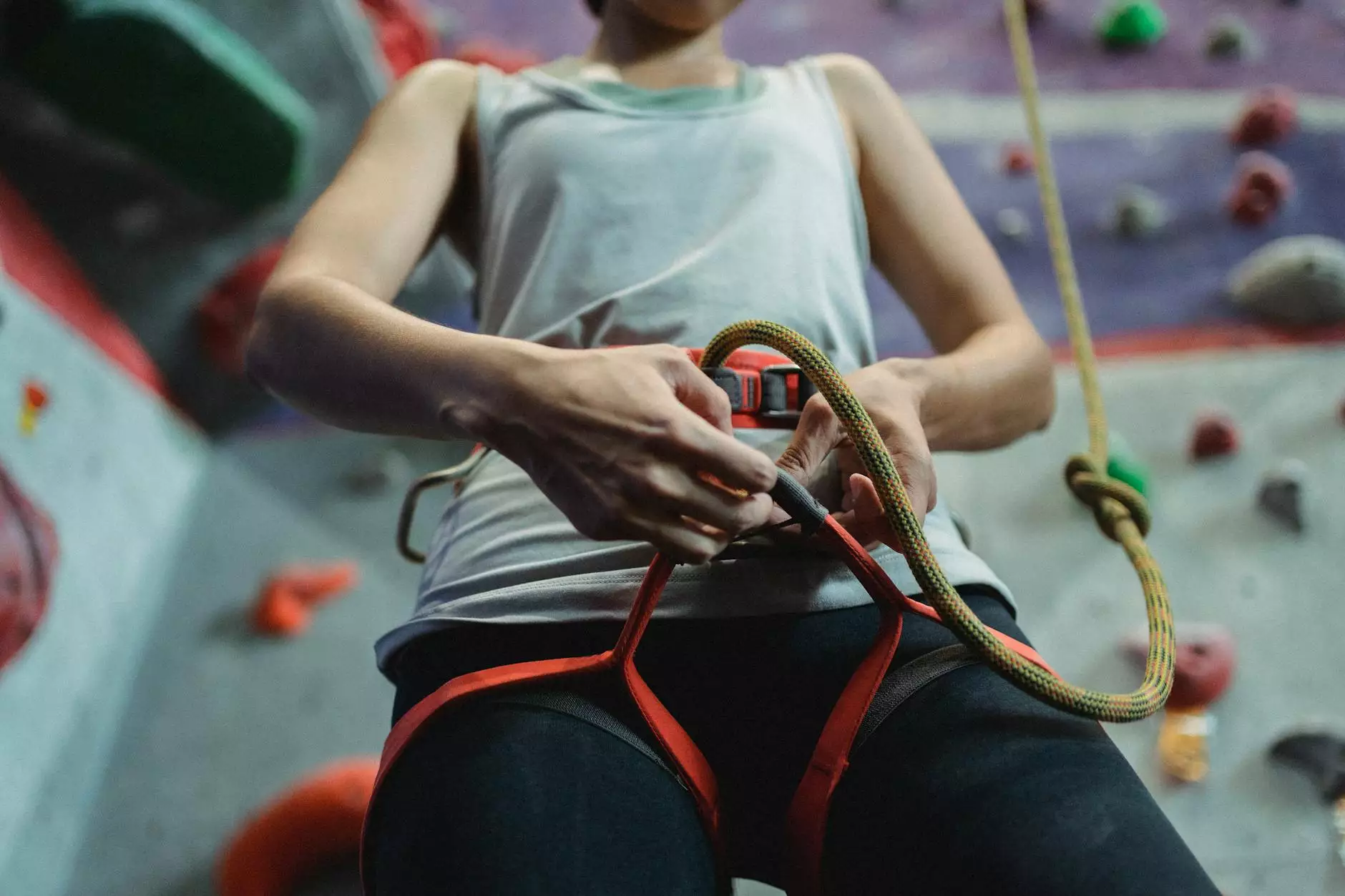
Welcome to our comprehensive guide on the components, challenges, and the critical role of quality standards in cable harness assembly quality control measures. As a leading provider of SEO services for businesses in the Business and Consumer Services industry, SEO in Sydney understands the importance of delivering high-quality content to optimally rank on search engines like Google.
Introduction to Cable Harness Assembly
Cable harness assembly plays a vital role in various industries, including automotive, aerospace, electronics, and telecommunications. It involves the process of connecting multiple cables and wires to form a unified and organized system. This ensures efficient transmission of signals, power, and data within complex electrical systems.
The Components Involved
A cable harness assembly typically comprises several components. These include:
- Cables and Wires: These are the basic building blocks of any cable harness assembly. They come in different types, sizes, and specifications depending on the application's requirements.
- Connectors: Connectors act as the interface between cables, wires, and other electrical or electronic devices. They ensure secure and reliable connections while allowing flexibility for maintenance and repairs.
- Terminals and Pins: Terminals and pins facilitate the connection between cables, wires, and connectors. They provide a reliable electrical connection, ensuring the smooth flow of signals and power.
- Protection Components: Cable harness assemblies may also include protective components such as heat shrink tubing, braided sleeves, and grommets. These components safeguard the cables and wires from environmental factors, mechanical stress, and potential damage.
- Labels and Markings: Proper labeling and marking of cable harness assemblies are essential for easy identification, maintenance, and troubleshooting.
Challenges in Cable Harness Assembly Quality Control
Ensuring the quality of cable harness assemblies is crucial to avoid potential failures, safety hazards, and performance issues. However, several challenges exist in maintaining stringent quality control measures. These challenges include:
- Complexity: Cable harness assemblies can be complex, with numerous cables, wires, and connectors involved. Proper assembly, alignment, and connection require meticulous attention to detail.
- Accuracy: Achieving precise alignment and connections is essential for optimal performance. Even minor errors can lead to significant issues, including signal interference and electrical failures.
- Testing: Thorough testing of cable harness assemblies is crucial to identify any defects or faulty connections. However, testing each assembly can be time-consuming and resource-intensive.
- Standardization: Standardizing cable harness assemblies is essential to ensure consistency and compatibility. However, different industries may have specific requirements and standards that need to be adhered to.
- Efficiency: Balancing quality control measures with production efficiency is a continuous challenge. Streamlining assembly processes without compromising quality is a delicate balance that needs to be achieved.
The Role of Quality Standards
To address these challenges, implementing and adhering to quality standards is paramount in cable harness assembly. Quality standards provide a framework for ensuring consistency, reliability, and performance. Some of the notable quality standards for cable harness assembly include:
- IPC/WHMA-A-620: The IPC/WHMA-A-620 standard provides guidelines and requirements for cable and wire harness assemblies. It covers assembly, materials, inspection criteria, and more.
- ISO 9001: ISO 9001 is a globally recognized quality management system standard. It focuses on various aspects of quality control, including process control, customer satisfaction, and continuous improvement.
- UL Certification: Underwriters Laboratories (UL) certification ensures that cable harness assemblies meet stringent safety standards. It provides confidence to end-users and regulatory bodies regarding the quality and safety of the product.
Conclusion
In conclusion, cable harness assembly plays a crucial role in various industries, and ensuring its quality is essential for optimal performance and safety. Overcoming the challenges of complexity, accuracy, testing, standardization, and efficiency requires adherence to quality standards such as IPC/WHMA-A-620, ISO 9001, and UL certification. At SEO in Sydney, we understand the intricacies of the Business and Consumer Services industry and provide expert SEO services to help businesses rank higher on search engines like Google. Contact us today to learn how we can enhance your online visibility and drive organic traffic to your website.