SolderTips: Issues With Incomplete Solder Reflow in Production
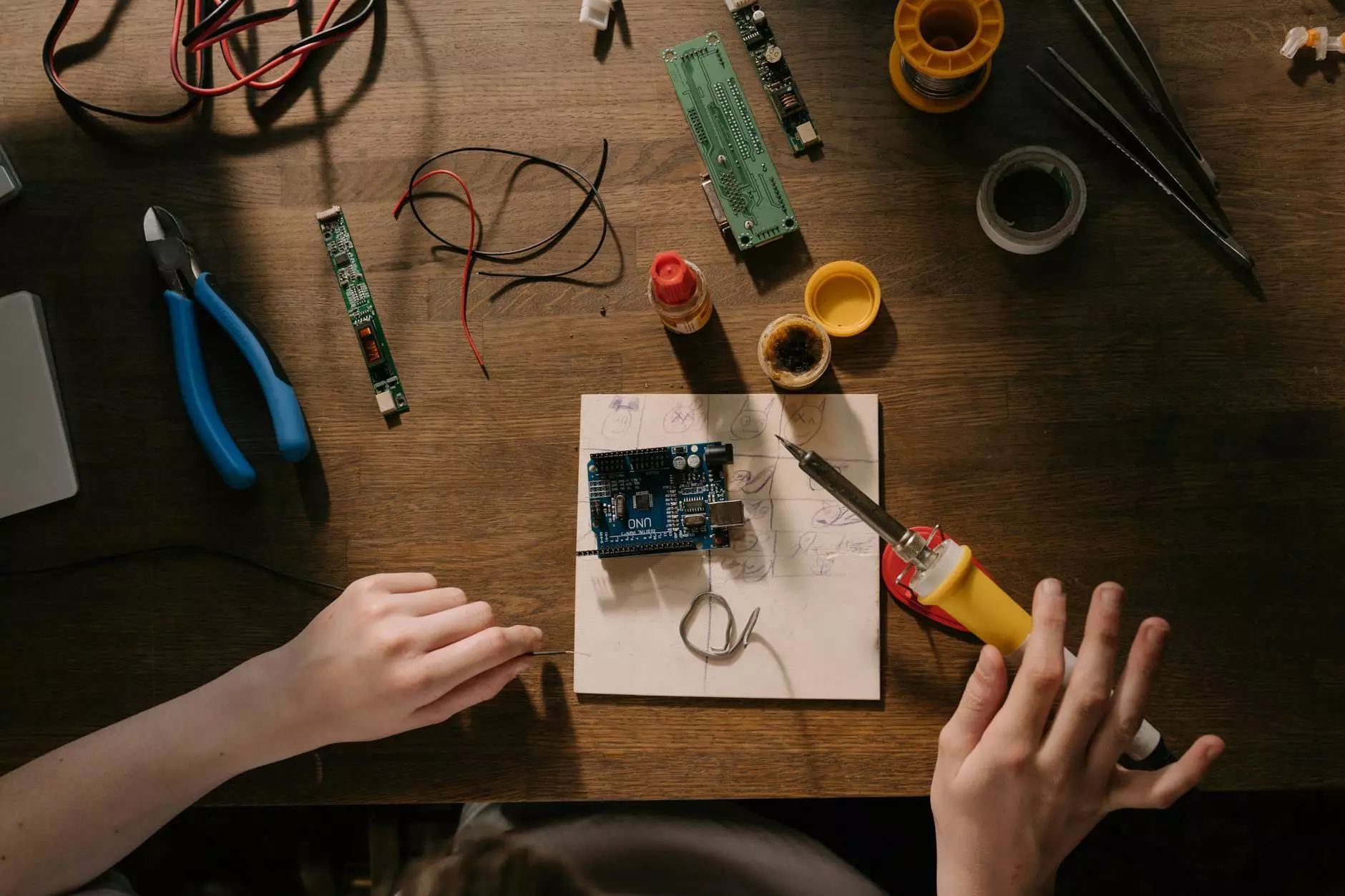
When it comes to the production of electronic components, achieving a successful solder reflow process is crucial. However, incomplete solder reflow can lead to numerous issues that affect the overall quality and functionality of the final product. In this article, we will dive into the common issues encountered during solder reflow in production and provide valuable insights on how to overcome them and ensure a successful solder reflow process.
1. Insufficient Preheating
Insufficient preheating is a common reason behind incomplete solder reflow. Inadequate preheating can result in temperature gradients across the board, causing certain areas to cool down rapidly during the solder reflow process. This creates temperature differentials, leading to incomplete solder reflow.
To overcome this issue, it is important to ensure proper preheating before initiating the solder reflow process. The preheating stage allows the board to reach and stabilize at a uniform temperature, reducing the chances of temperature differentials and promoting complete solder reflow.
2. Incorrect Time-Temperature Profile
Another crucial factor that affects solder reflow is the time-temperature profile. Incorrect settings of the time and temperature parameters can result in incomplete solder reflow and yield poor solder joints.
To optimize the time-temperature profile, thorough research and understanding of the specific solder paste's requirements and manufacturer recommendations are essential. It is important to carefully configure the reflow oven settings to match the solder paste's specifications, ensuring optimal temperature ramp-up and dwell time, thus achieving complete solder reflow.
3. Insufficient Flux Activity
Insufficient flux activity is another primary cause of incomplete solder reflow. Flux plays a crucial role in solder wetting and spreading, facilitating the formation of strong and reliable solder joints. Inadequate flux activity can result in poor wetting and incomplete solder reflow, leading to weak and unreliable connections.
To address this issue, it is important to ensure the use of high-quality solder paste with an appropriate level of flux activity. Choosing a solder paste with a higher flux content can enhance flux activity, promoting complete solder reflow and enabling robust solder joint formation.
4. Component Misalignment
Component misalignment can also contribute to incomplete solder reflow. When components are not properly aligned on the board, it can hinder the solder paste's proper application and distribution, leading to incomplete solder joints.
To mitigate this issue, it is crucial to ensure accurate component placement and alignment during the manufacturing process. Implementing advanced technologies such as automated optical inspection (AOI) systems can aid in detecting any misalignment issues and rectifying them before the solder reflow process, ensuring proper solder joint formation and complete solder reflow.
5. Insufficient Solder Paste Volume
The amount of solder paste applied to the board plays a significant role in achieving complete solder reflow. Insufficient solder paste volume can result in incomplete solder joints and weak connections.
To prevent this issue, it is vital to carefully optimize the solder paste printing process. Ensuring precise solder paste deposition and maintaining consistent volume across the board can help achieve complete solder reflow and enhance the overall solder joint quality.
6. Inadequate Cleaning
Inadequate cleaning of the board after the solder reflow process can also lead to incomplete solder reflow. Residual flux or other contaminants left on the board surface can hinder the formation of strong, reliable solder joints.
To address this issue, thorough cleaning processes should be implemented after the solder reflow process. This includes the use of appropriate cleaning agents and techniques to remove any residues, ensuring the optimal condition for the soldered components and achieving complete solder reflow.
Conclusion
In conclusion, ensuring a successful solder reflow process is crucial for the production of high-quality electronic components. Understanding and addressing common issues like insufficient preheating, incorrect time-temperature profiles, insufficient flux activity, component misalignment, insufficient solder paste volume, and inadequate cleaning are essential steps towards achieving complete solder reflow and reliable solder joint formation.
By implementing best practices and careful optimization of the solder reflow process, manufacturers can minimize the occurrence of incomplete solder reflow and produce electronic components of exceptional quality and reliability.