3D Printing Creates New Possibilities for PCB Manufacturing Methods
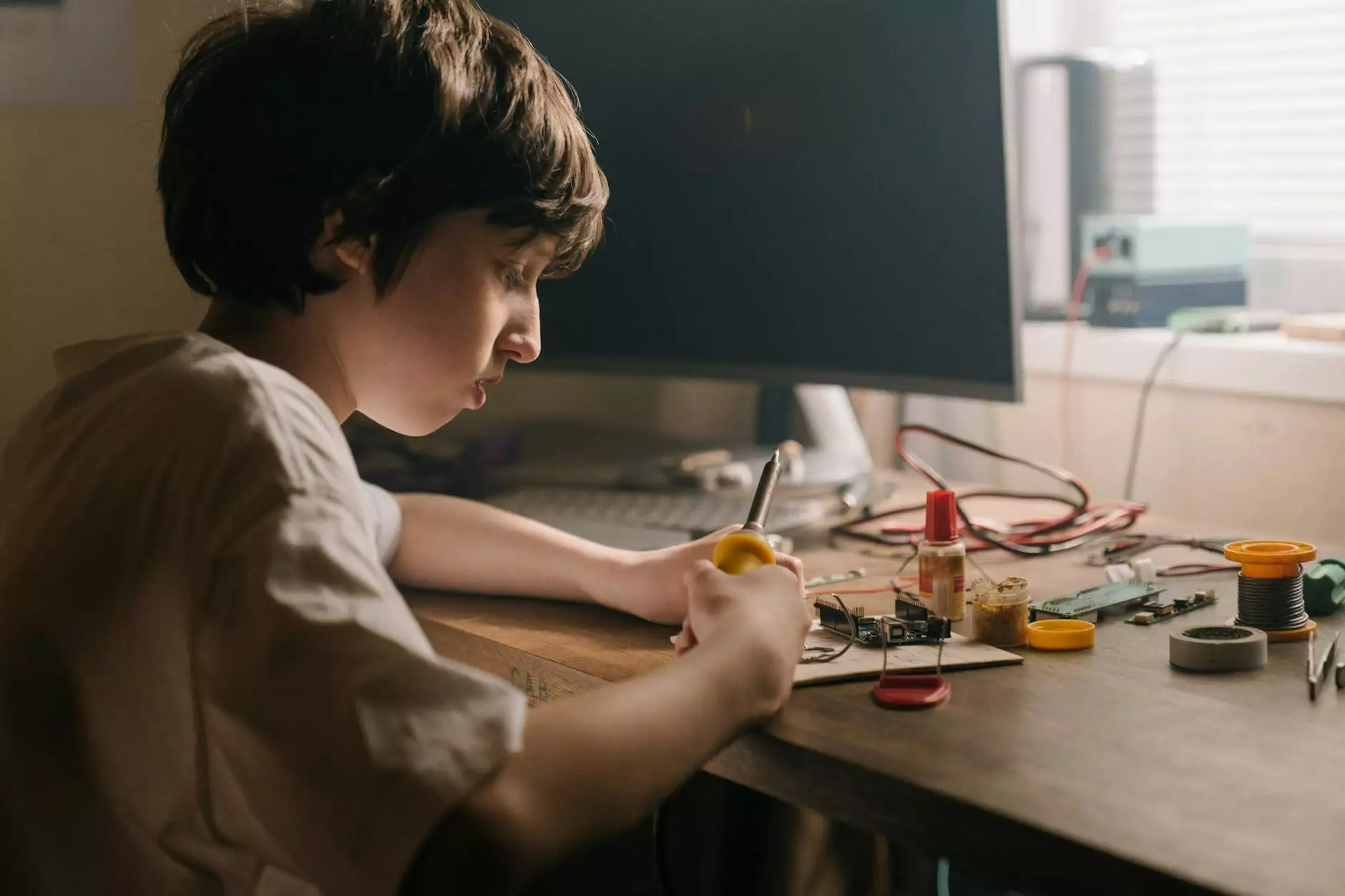
Introduction
In the ever-evolving world of technology, 3D printing has emerged as a groundbreaking innovation that is rapidly reshaping industries across the globe. One such industry that is significantly benefiting from 3D printing is PCB (Printed Circuit Board) manufacturing.
What is PCB Manufacturing?
Before diving into the profound impact of 3D printing on PCB manufacturing, let's first understand what PCB manufacturing entails. PCBs are essential components used in electronic devices to provide mechanical support and electrical connections. Traditional methods of PCB manufacturing involve complex and time-consuming processes, including etching copper layers, drilling holes, and soldering components.
The Emergence of 3D Printing in PCB Manufacturing
3D printing, also known as additive manufacturing, has revolutionized the PCB manufacturing process by introducing a new level of efficiency, customization, and design flexibility. With the ability to create three-dimensional objects layer by layer, 3D printing has opened up immense possibilities for PCB production.
Benefits of 3D Printing in PCB Manufacturing
1. Design Flexibility: 3D printing allows designers to create intricate and complex PCB designs that were previously challenging or impossible to achieve with traditional manufacturing methods.
2. Rapid Prototyping: The rapid prototyping capabilities of 3D printing enable PCB designers to quickly iterate and refine their designs, reducing time-to-market and costs associated with traditional prototyping methods.
3. Cost Efficiency: With 3D printing, the need for multiple manufacturing steps and complex tooling is reduced, resulting in cost savings in the PCB manufacturing process.
4. Customization: 3D printing allows for tailored and customized PCB designs, catering to the specific requirements of individual projects or products.
5. Reduced Waste: Traditional manufacturing methods often generate significant waste material, whereas 3D printing is an additive process, minimizing material wastage.
Applications of 3D Printing in PCB Manufacturing
1. Rapid Prototyping
The ability to quickly produce functional prototypes using 3D printing has transformed the way PCB designs are tested and validated. Designers can now efficiently identify and correct any design flaws or improvements before mass production, minimizing costly errors and delays.
2. Complex Geometries
3D printing enables the creation of intricate geometric shapes and designs that were previously challenging to produce using traditional manufacturing techniques. This capability opens up new avenues for designers to optimize their PCB layouts, leading to improved electrical performance and enhanced functionality.
3. Miniaturization
As electronics continue to shrink in size, 3D printing plays a crucial role in manufacturing miniaturized PCBs. The precise and accurate nature of 3D printing ensures that intricate connections and components can be successfully incorporated, even in tight spaces.
4. Customized Interfaces
3D printing allows for the creation of unique and customized PCB interfaces, enabling seamless integration with other electronic components. This level of customization offers enhanced user experience and functionality, making it an ideal choice for various industries.
Conclusion
As the capabilities of 3D printing continue to expand, the PCB manufacturing industry stands to benefit immensely from this revolutionary technology. The ability to create complex designs, reduce costs, customize interfaces, and accelerate prototyping has opened up new dimensions for the electronics industry. Embracing 3D printing in PCB manufacturing is not only a competitive advantage but also a step towards unlocking new possibilities and driving innovation.